- Aug 12, 2020
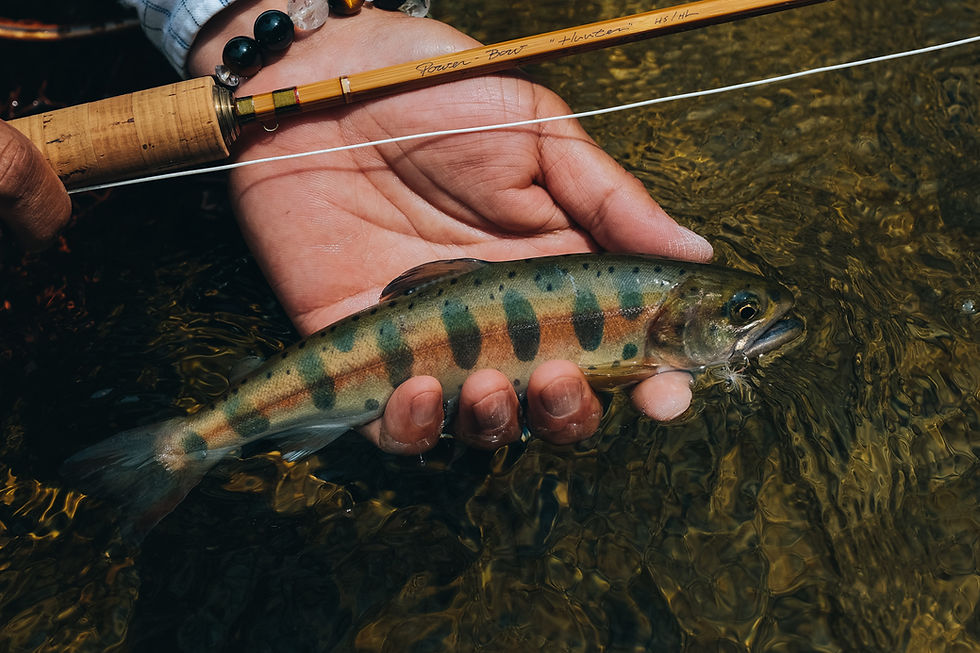
Tadanobu’s Genius rod is designed to cast a size #12 fly to the distance of over 10 yards. He never uses long leaders such as over 15 feet.
“I did almost everything. I used to be a long leader believer, a cherry trout (sea-run yamame trout) chaser fishing with a Spey rod (if you catch one fish in a season, you are lucky), a headwater lover. I was even an owner of a fly shop. After all these crazy things, I found myself lost somewhere in the fly fishing world.”
It was eighteen years ago when Tadanobu decided to get off the fly fishing merry-go-round. He started making bamboo rods. At his very beginning, he decided to follow the concept of “High Speed, High Line,” which is, of course, Charles Ritz’s doctrine. As a natural consequence, he targeted Pezon et Michel.
There is no bamboo rod maker who started his career without copying the old famous makers’ rods, such as Leonard, Payne, and Garrison. Pezon et Michel is still popular in Japan though it might be in the minority if we look around the world.
*This article was extracted from “Mostly Bamboo” by courtesy of the author.